大型鍛件熱處理中斷裂的因素及其產(chǎn)生的情況?
在大型鍛件的熱處理中,尤其是在粹火過程中,經(jīng)常會碰到斷裂問題,斷裂形式有橫裂、縱裂、脫肩、置裂、剝落、龜裂等。而其斷裂原因是極其復(fù)雜的,往往是多種因素作用的結(jié)果,但從總的方面來考慮不外是兩方面的因素:一是內(nèi)應(yīng)力(拉應(yīng)力)超過材料的實(shí)際破斷強(qiáng)度,二是雖然內(nèi)應(yīng)力并不過高,但由于材料本身的缺陷造成材料強(qiáng)度下降。以下就從這兩方面來分析一下大鍛件裂紋產(chǎn)生的情況。
(一)橫裂
形成橫向裂紋時內(nèi)應(yīng)力分布的特征是:表面受壓應(yīng)力,離表面一定的距離應(yīng)力發(fā)生劇變,由壓應(yīng)力變?yōu)楹艽蟮睦瓚?yīng)力。裂紋產(chǎn)生在拉應(yīng)力峰值區(qū)域內(nèi),然后當(dāng)內(nèi)應(yīng)力重新分布或鋼的脆性進(jìn)一步增加時才蔓延到工件表面。橫向裂紋的特點(diǎn)是垂直于軸的方向,這類裂紋往往發(fā)生在未淬透的工件中,因?yàn)榇阌才c未淬硬的過渡區(qū)有一個大的應(yīng)力峰值,而且軸向應(yīng)力大于切向應(yīng)力。
大型鍛件因不可能全部淬透,而且往往存在較嚴(yán)重的冶金缺陷(如氣泡、夾雜、銀造裂紋、偏析、白點(diǎn)等),在熱處理寵力作用下,以這些缺陷為裂紋的起點(diǎn),緩慢擴(kuò)張直到最后突然斷裂。另外在軋棍的橫斷實(shí)例中,往往在斷裂面上不能看出明顯的斷裂起點(diǎn),這像刀切的一樣,這是較脆的材料在熱應(yīng)力作用下引起斷裂的特征。
對軸類鍛件來說,打中心孔并對表面和中心一起冷卻,可使拉應(yīng)力的峰值移向中間層,數(shù)值也可大大降低,所以這是防止橫斷的有效方法之一。然而打中心孔時往往會使冶金缺陷暴露到中心孔表面,亦有其不利之處。

(二)縱裂
裂紋產(chǎn)生于工件表面附近最大拉應(yīng)力處并裂向心部有較大深度的裂痕,裂紋的走向一般平行于軸向,但是工件存在應(yīng)力集中部位或內(nèi)部組織缺陷等,裂紋也可能改變走向,在完全淬透的工件中容易產(chǎn)生縱向裂紋,這與淬透工件的表層存在較大的切向拉應(yīng)力有關(guān),并且隨碳含量的提高,形成縱向裂紋的傾向增大。低碳鋼因馬氏體比容小,而且熱應(yīng)力作用強(qiáng),表面存在很大的殘余壓應(yīng)力是不易淬裂的。隨著碳含量的提高,表面壓應(yīng)力減少(組織應(yīng)力作用增強(qiáng)),拉應(yīng)力峰值移向表面,碳含量高的馬氏體其破斷抗力降低,因此高碳鋼在過熱的情況下淬裂的傾向增大。
工件尺寸直接影響淬火后殘余應(yīng)力大小和分布,直徑小的工件因表層與心部的溫差小,淬火時應(yīng)力也小,故不易淬裂。在淬透的情況下,隨著直徑增大,一方面悴火后的殘余應(yīng)力值增加,另一方面卻由于拉應(yīng)力峰值逐步遠(yuǎn)離表面,則有利于阻止表面裂紋的產(chǎn)生。由此看來,對工件淬透的情況下有一個淬裂的敏感尺寸,接近此尺寸的工件有淬裂的危險。實(shí)踐經(jīng)驗(yàn)表明,碳素鋼淬火時的危險尺寸約為8~15mm,低合金鋼油淬的危險尺寸約為25~40mm。
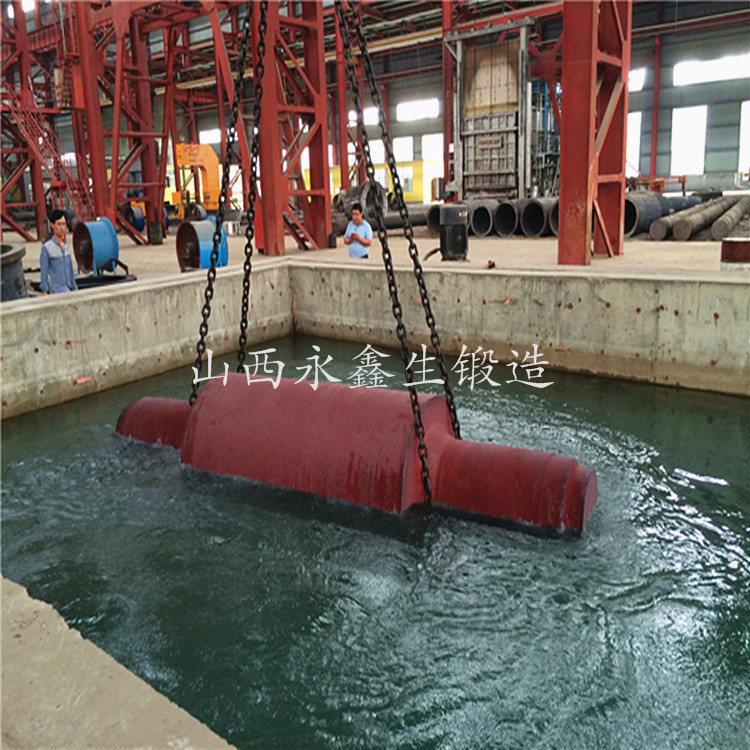
(三)置裂
零件在熱處理終了后,在長時間放置中發(fā)生自然破斷的現(xiàn)象稱為置裂。產(chǎn)生置裂的主要原因是內(nèi)應(yīng)力與氫氣的聯(lián)合作用和殘余奧氏體的分解。
目前在考慮氫和應(yīng)力的聯(lián)合作用時,認(rèn)為氫原子在應(yīng)力的作用下,將向缺陷尖端處有應(yīng)力集中的三向拉應(yīng)力處聚集,沉淀在位錯線上,對位錯起釘扎作用,使它不能自由運(yùn)動,導(dǎo)致材料產(chǎn)生局部硬化。隨后在外力或內(nèi)應(yīng)力的繼續(xù)作用下,在局部硬化區(qū)產(chǎn)生裂紋并逐漸發(fā)展長大。當(dāng)裂紋長大到貧氫區(qū)后,位錯線的運(yùn)動恢復(fù)自由,基體可以通過塑性變形使應(yīng)力松弛,裂紋長大停止。以后隨著時間的延長,氫原子在應(yīng)力的作用下重新在裂紋前沿集結(jié),材料又產(chǎn)生局部硬化,裂紋又繼續(xù)長大。這一過程不斷重復(fù),裂紋一段一段擴(kuò)大,最后導(dǎo)致突然斷裂,由此可見,這種脆斷過程是為氫原子在應(yīng)力作用下的擴(kuò)散所控制。
當(dāng)熱處理后工件中含有較多的殘余奧氏體時,由于殘余奧氏體分解,發(fā)生體積膨脹和氫的溶解度突然下降,引起了內(nèi)應(yīng)力增加和氫脆作用加劇,亦將導(dǎo)致置裂。
防止置裂的方法主要是減小鋼中的內(nèi)應(yīng)力和氫氣含量,使之不至于引起破斷。